Direct Reduction Iron | Paralloy
Products & Solutions
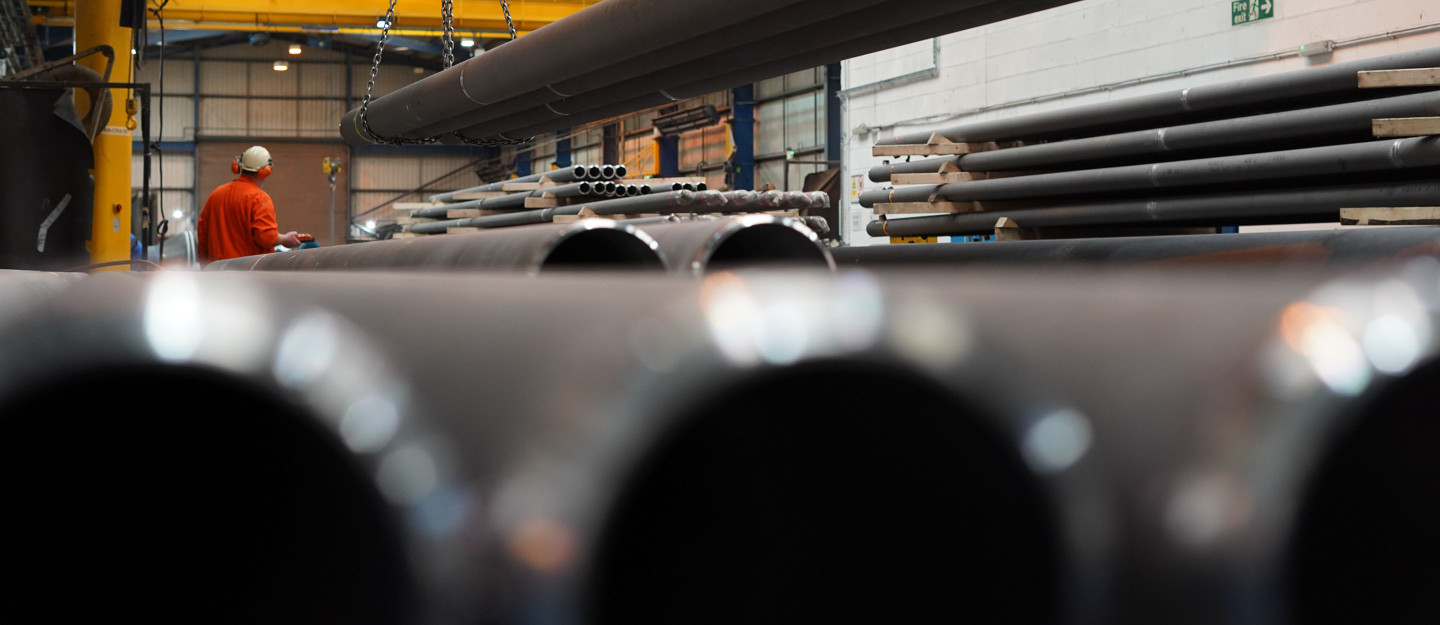
Markets
Direct Reduction Iron | Paralloy
In the production of reforming gas for the DRI plants, one of the strategic pieces of equipment of the plant is the reformer furnace and the Process Gas Heaters. The reformer tubes inside that furnace are designed in dimensions to stand for a minimum of 100,000 hours at approximately 1050°C TMT, and up to 2.5 bars of pressure in the case of the Midrex reformers tubes type. The key features we ask those tubes to have are creep resistance at higher and higher temperatures, and to a degree, ability to withstand thermal cycles.
Paralloy alloys have tailored chemistry that enables exposure to
temperatures up to 1200°C. Most specifically, they demonstrate very low
creep rates that allow for long exposure to high in-service
temperatures.
Talk to us today about our ground-breaking
technologies and solutions, which are designed to endure the extreme
conditions found within the DRI industry.
Direct Reduction Iron | Paralloy
Products & Solutions
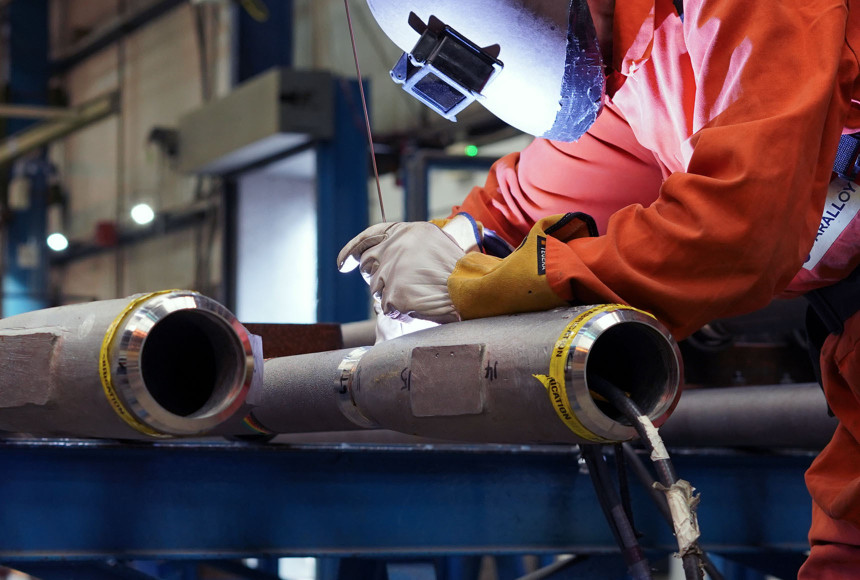
Direct Reduction Iron | Paralloy
DRI Process Gas Heaters and Steam Reforming Tube
Process Gas Heater: We offer a comprehensive range of alloys specially developed to be installed in the Process Gas Heaters: radiant coil with bespoke high creep resistance (H46M) and low carbon (CR39W) material.
Talk to our experts Paralloy Products & Materials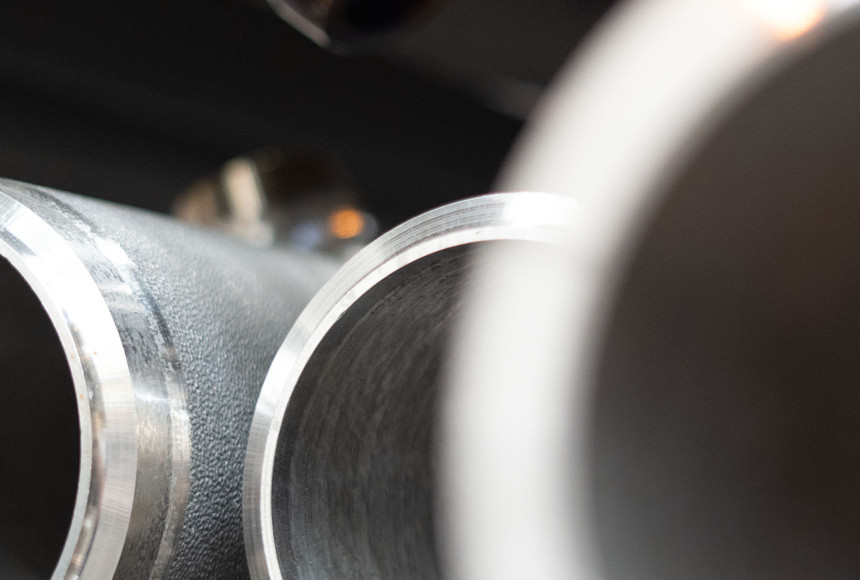
Direct Reduction Iron | Paralloy
Midrex Type Reformer Tubes
PARALLOY RED+ and RED W are variations of existing petrochemical alloys specially developed for the DRI application related to Midrex type reformer designs those alloys have the multi abilities to have good creep resistance, low creep rate, good aged ductility to allow a long tube life, with minimisation of tube elongation with time still avoid any dramatic sudden crack formation during unpredicted events
Talk to our experts Paralloy Products & Materials